Plastic welding is a process that involves joining together two or more pieces of plastic using heat and pressure. People worldwide use this method for manufacturing and repairing various plastic products. Including automotive parts, household appliances, and toys. This guide will provide a detailed overview of the different methods and techniques. Which is used for beginner plastic welding and the tools and equipment needed to start. We will also cover some important considerations for achieving solid and durable welds and provide tips for troubleshooting common problems. Let’s get to the beginner’s guide to plastic welding.
The choice of method for plastic welding will depend on the type and thickness of the plastic. And the size and shape of the pieces being joined. It is possible to use several different tools and techniques.
- Types of Plastic Welding
- Tools and Equipment for Plastic Welding
- Considerations for Strong, Durable Plastic Welding
- Troubleshooting Common Problems of Plastic Welding
- Selecting the appropriate plastic material
- Advantages and disadvantages of plastic welding
- Plastic welding compatibility chart
- Plastic welding kit
- What type of plastic you can’t weld
- How long does plastic weld last
- Ultrasonic Plastic Welding Compatibility
- Identify the Types of Plastic
- Final Thoughts
Types of Plastic Welding
There are several types of plastic welding, including hot plate, hot gas, ultrasonic, and spin welding. Each type of welding has its advantages, depending on the type of plastic and the application.
Hot plate welding is the most common type because it is fast and easy to use. On the other hand, ultrasonic welding is best for joining plastics with different melting points. In this beginners guide to plastic welding, let’s discuss the 6 main types of plastic welding.
- Hot gas welding
- Ultrasonic welding
- Vibration welding
- Spin welding
- Laser welding
- Electrofusion welding
Each method involves applying different amounts of heat and pressure to the plastic to create a bond between the pieces.
Hot Gas Welding
Hot gas welding, also known as hot air welding, is a method that involves using a stream of hot, compressed air to melt and join the plastic pieces together. This method is for welding thin plastic sheets and is suitable for a wide range of thermoplastics. The process begins by preparing the plastic pieces by cleaning and drying them and then clamping them together in the desired position.
Ultrasonic Welding
Ultrasonic welding is a method that uses high-frequency sound waves to generate heat and pressure, causing the plastic to melt and bond together. This method is for welding small, intricate parts or joining thin plastic sheets.
The process begins by preparing the plastic pieces by cleaning and drying them and then placing them in a particular welding fixture. There is an ultrasonic horn to apply high-frequency vibrations to the plastic, causing it to melt and bond together.
Vibration Welding
Vibration welding is a method that involves using vibrations to generate heat and pressure, causing the plastic to melt and bond together. A large, thick piece of plastic, such as an automotive part, is welded using this method.
The process begins by preparing the plastic pieces by cleaning and drying them and then clamping them together in the desired position.
Spin Welding
Spin welding is a method that involves rotating one of the plastic pieces and applying pressure to the other piece, causing the plastic to melt and bond together. This method is for welding cylindrical parts, such as toy figurines.
The process begins by preparing the plastic pieces by cleaning and drying them and then placing them in a particular welding fixture. One of the pieces is then rotated while the other is held in place. Causing the plastic to melt and bond together.
Laser Welding
Laser welding is a method that uses a focused beam of light to generate heat and pressure, causing the plastic to melt and bond together. This method is for welding small, intricate parts or joining thin plastic sheets.
The process begins by preparing the plastic pieces by cleaning and drying them and then placing them in a unique welding fixture. A laser is then directed onto the plastic, generating heat and melting the edges to create a bond as the plastic cools.
Electrofusion Welding
Electrofusion welding is a method that involves applying an electrical current to the plastic to generate heat and pressure, causing the plastic to melt and bond together. This method is for welding pipes and fittings made of thermoplastic materials.
The process begins by preparing the plastic pieces by cleaning and drying them and then attaching special electrofusion fittings to the ends of the pipes. An electrical current passes through the fittings, causing the plastic to melt and bond.
Tools and Equipment for Plastic Welding
The tools and equipment needed for plastic welding will depend on the method used. However, some everyday items are helpful for most methods, including:
- Plastic welding gun or welding torch
- Welding rod or filler material
- Welding clamp or vise
- Protective goggles
- Heat gun or oven (for preheating)
- Grinding and finishing tools (such as files and sandpaper)
Using the proper tools and equipment for the specific type of plastic is essential. Using the wrong tools or techniques can result in weak or ineffective welds.
Considerations for Strong, Durable Plastic Welding
Several important factors to consider when creating solid and durable welds using plastic welding techniques. These include:
Cleanliness
It is crucial to ensure that the plastic pieces that will be welded are clean and dry. Any dirt or moisture can weaken the bond.
Heating
The plastic must be heated to the proper temperature for the weld to be effective. Too low of a temperature can result in a weak weld, while too high of a temperature can cause the plastic to become brittle or distorted.
Pressure
Applying the proper pressure is essential for achieving a robust and durable weld. Too little pressure can result in a weak bond, while too much pressure can cause the plastic to become distorted.
Cooling
Allowing the welded plastic to cool slowly and evenly is important for achieving a strong, durable bond. Rapid cooling can cause the weld to become weak or brittle.
Troubleshooting Common Problems of Plastic Welding
There are a few common problems that can arise when attempting to weld plastic, including:
Weak or brittle welds: This can be caused by improper heating, pressure, or plastic cooling.
Distorted or misshapen plastic: This can be caused by applying too much heat or pressure. Or by cooling the plastic too quickly.
Cracks or voids in the weld: This can be caused by dirt or moisture on the plastic. Or using the wrong filler material.
Carefully follow the recommended techniques and guidelines for the specific type of welded plastic. And the method used is important for troubleshooting these problems. It may also be helpful to seek the advice of an experienced plastic welder or refer to specialized welding resources for further guidance.
Selecting the appropriate plastic material
One important aspect of plastic welding we did not cover in this guide is selecting the appropriate plastic material for the specific application. Different types of plastic have different properties and characteristics, and it is important to choose a material that is suitable for the intended use. Consulting with a plastic supplier or engineer can help determine the best material for a particular application.
Advantages and disadvantages of plastic welding
Here are some advantages and disadvantages of the different types of plastic welding.
Advantages of Plastic Welding
- Strong and durable bonds
- Versatility
- Cost-effective compared to other types of welding
- Minimal heat-affected zone
- Use in a variety of industries
Disadvantages of Plastic Welding
- Requires specialized equipment and training
- Limited to thermoplastics, not suitable for thermosetting plastics
- Surface preparation is crucial for achieving a solid bond
- Some types of plastic welding emit fumes that can be harmful to inhale
- Plastic Welding may not be suitable for high-temperature or high-pressure applications.
Plastic welding compatibility chart
Square means good compatibility between the two plastics. Which can be welded by ultrasonic easily. Circle means the two plastics can be compatible with acceptable welding performance under some circumstances. Space means the compatibility of the two plastics are terrible; they are difficult being weld by ultrasonic.
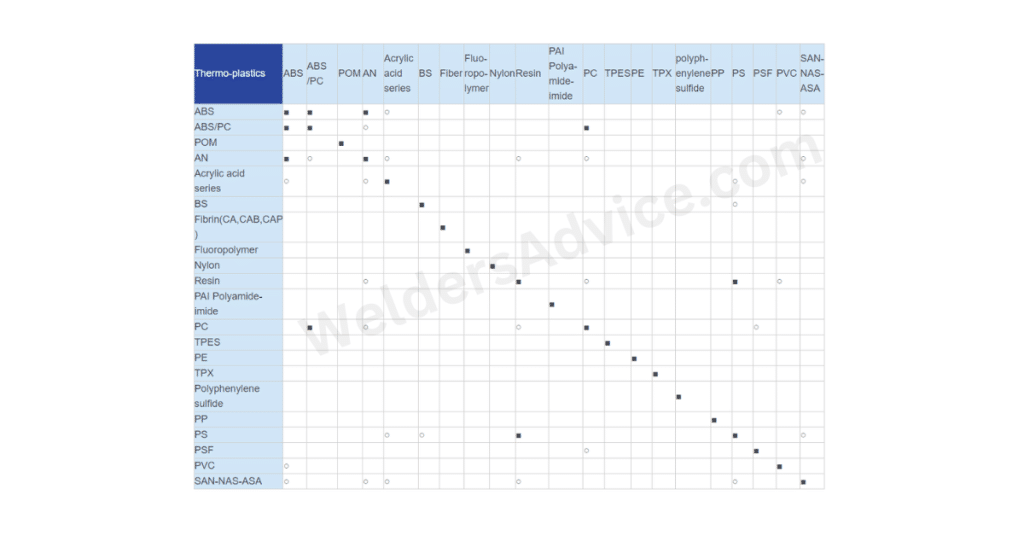
Also Read: Advantages and Disadvantages of Plastic Welding
Plastic welding kit
A plastic welding kit is a must-have for anyone looking to take on the art of plastic welding. This comprehensive set of tools offers everything needed, including a plastic welder, welding rods, and accessories. The welder uses a specially designed heat gun, and the rods are available in several different thicknesses and materials to suit different projects. With the right supplies and instruction, anyone can become a master of plastic welding!
What type of plastic you can’t weld
You can’t weld some types of plastics, including polyethylene and polypropylene. These materials are too soft and flexible. And must be joined using adhesives or mechanical fasteners. Additionally, certain types of plastic may require specialized welding techniques or special welding rods and equipment.
How long does plastic weld last
Plastic welds typically last for the life of the plastic, depending on the type of plastic and the application. For example, plastic welds used in automotive applications can last for many years, while plastic welds used in medical applications may not last as long.
Additionally, the quality of the plastic weld can also affect its longevity. Poorly executed welds may be more prone to cracking or failure. To ensure a long-lasting plastic weld, it is important to use high-quality materials and welding techniques.
Ultrasonic Plastic Welding Compatibility
Ultrasonic welding is a viable option for plastic welding, and compatibility of different types of plastic materials is imperative for a successful weld. The most compatible plastics for ultrasonic welding are PVC, polycarbonate, PTFE, nylon, and ABS. Heat-sensitive materials such as polyethylene and polypropylene may require unique settings and precautions, so it is important to research to ensure the plastic is compatible. With the correct settings and materials, ultrasonic welding provides a reliable seal without additional fasteners.
Identify the Types of Plastic
The most common method of identifying types of plastic is by looking at its recycling symbol. Each type of plastic is assigned a specific number. This number can be found on the bottom of the plastic item and is usually followed by a letter. For example, PET plastic has a recycling symbol of 1, and HDPE plastic has a recycling symbol of 2. Knowing the recycling symbol of plastic can help identify which type of plastic it is. Some plastics have special codes that can be used to identify them, such as “PC” for polycarbonate.
Final Thoughts
Plastic welding is a versatile and widely used method for manufacturing and repairing various plastic products. By understanding the different methods and techniques, as well as the tools and equipment needed, it is possible to achieve strong, durable welds and troubleshoot common problems. With the proper knowledge and skills, plastic welding can be a valuable tool for many applications. I hope these beginners guide to plastic welding helps you to achieve your goal.