One of the most important components of a Mig welder is the contact tip. The contact tip is responsible for transferring the electrical current from the welding machine to the welding wire. Which then melts and fuses with the metal being welded. The 025 Mig Welder contact tip is a specific type of contact tip that is designed for use with 0.025-inch welding wire.
- Why are 025 Mig Welder Contact Tips important?
- How to choose the right size contact tip for your Mig Welder?
- Advantages of using 025 Mig Welder Contact Tip
- Precision welding
- Reduced spatter
- Improved productivity
- Longer contact tip life
- Consistent weld quality
- Reduced downtime
- How to install or replace 025 Mig Welder Contact Tips?
- Common problems associated with 025 Mig Welder Contact Tips
- How to troubleshoot 025 Mig Welder Contact Tips?
- What is the role of a 025 Contact Tip in Mig Welding?
- Final Thoughts
Why are 025 Mig Welder Contact Tips important?
Contact tips are one of the most critical components of a Mig welding gun. They help to guide the wire electrode and maintain consistent electrical contact between the wire and the welding gun. Therefore, a stable electrical connection is essential for maintaining a steady welding arc and achieving high-quality welds.
The diameter of the contact tip also plays a crucial role in the welding process. The size of the contact tip should match the diameter of the wire electrode being used. Using the wrong size contact tip can lead to inconsistent welds and increased spatter.
How to choose the right size contact tip for your Mig Welder?
When choosing the right size contact tip keep in mind to achieve high-quality welds. The size of the contact tip should match the diameter of the wire electrode being used. However, the wire electrode diameter is typically stamped on the spool of the welding wire.
Here are some general guidelines for choosing the right size contact tip:
- For welding wire with a diameter of 0.023 inches, use a 0.023-inch contact tip.
- For welding wire with a diameter of 0.030 inches, use a 0.030-inch contact tip.
- For welding wire with a diameter of 0.035 inches, use a 0.035-inch contact tip.
- For welding wire with a diameter of 0.045 inches, use a 0.045-inch contact tip.
It’s essential to follow the manufacturer’s recommendations for the size of the contact tip to use for your specific Mig welding machine.
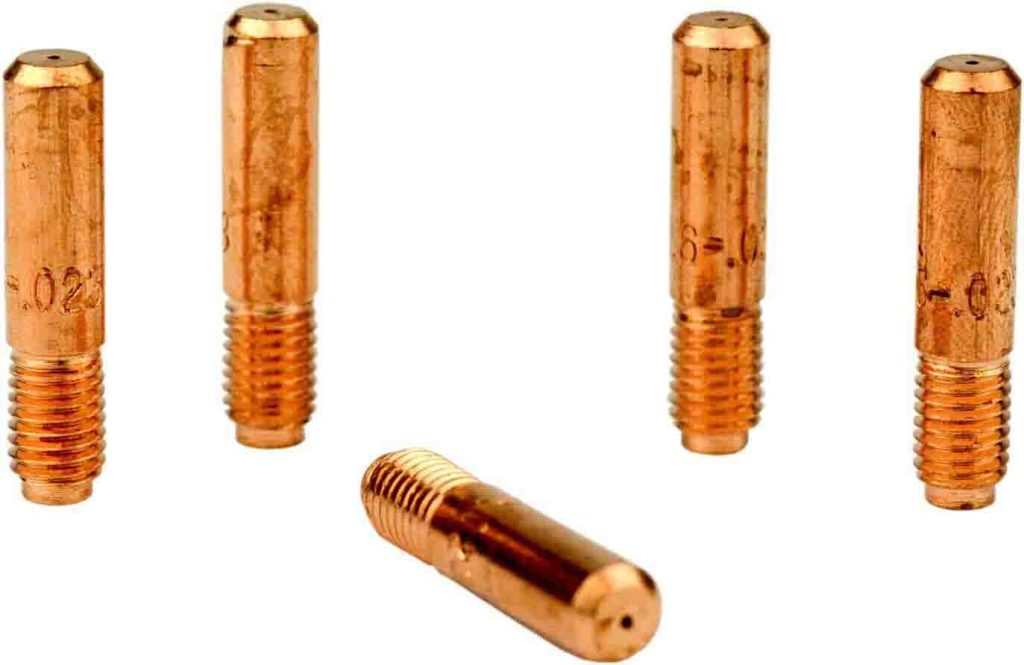
Advantages of using 025 Mig Welder Contact Tip
There are several advantages of using 025 Mig Welder Contact Tips. Some of them include:
Precision welding
025 Mig Welder Contact Tips provide a precise and stable arc, which is crucial for welding small and delicate parts.
Reduced spatter
Using the right size contact tip can help reduce spatter, which saves time and reduces the need for post-weld cleanup.
Improved productivity
A stable arc and reduced spatter can lead to increased productivity and efficiency in the welding process.
Longer contact tip life
Using the correct size and material for your contact tips can help extend their life, reducing the need for frequent replacements.
Consistent weld quality
The use of the proper contact tip size ensures that the weld quality remains consistent throughout the welding process.
Reduced downtime
Using high-quality contact tips can reduce the need for frequent replacements. Which results in less downtime for your welding operations.
How to install or replace 025 Mig Welder Contact Tips?
Installing or replacing 025 Mig Welder Contact Tips is a simple process. Follow these steps:
- Turn off the Mig welding machine and disconnect the welding gun from the power source.
- Remove the nozzle from the end of the welding gun.
- Remove the old contact tip by pushing it out of the end of the welding gun.
- Insert the new 025 Mig Welder Contact Tip into the end of the welding gun and make sure it’s seated firmly.
- Replace the nozzle and tighten it securely.
- Reconnect the welding gun to the power source and turn on the Mig welding machine.
Common problems associated with 025 Mig Welder Contact Tips
Mig Welder Contact Tips are prone to wear and tear due to their constant use in the welding process. Some common problems associated with Mig Welder Contact Tips include:
Burnback
This occurs when the wire electrode melts and fuses to the contact tip, causing it to stick to the gun. Burnback can be caused by incorrect wire feed speed or voltage settings.
Tip spatter
Tip spatter occurs when small molten droplets of metal stick to the contact tip and can be caused by incorrect welding parameters, such as high voltage or wire feed speed.
Contact tip wear
The constant friction and heat generated during welding can cause the contact tip to wear out over time. This can lead to inconsistent welds and the need for frequent replacement.
Wire feed issues
Wire feed problems can occur when the contact tip is clogged with spatter or debris, causing the wire to jam or feed erratically.
How to troubleshoot 025 Mig Welder Contact Tips?
If you’re experiencing problems with your Mig Welder Contact Tips, here are some troubleshooting steps to follow:
Burnback
If you’re experiencing burn back, first check the wire feed speed and voltage settings. If they’re incorrect, adjust them accordingly. You should also check the condition of the contact tip. If it’s worn or damaged, replace it with a new one.
Tip spatter
Tip spatter can be caused by incorrect welding parameters, such as high voltage or wire feed speed. Check your settings and adjust them as necessary. You should also inspect the contact tip for damage or wear. If it’s worn or damaged, replace it with a new one.
Contact tip wear
If your contact tip is wearing out too quickly, check your welding parameters to ensure they’re correct. You should also check the wire feed speed to make sure it’s not too high. If the wire feed speed is too high, it can cause the contact tip to wear out faster. Replace the contact tip with a new one if it’s worn or damaged.
Wire feed issues
If you’re experiencing wire feed issues, it’s important to check the condition of the contact tip. Specifically, it may be clogged with spatter or debris, which can cause the wire to jam or feed erratically.
Therefore, it’s recommended to clean the contact tip with a wire brush and replace it with a new one if necessary. By doing so, you can ensure proper wire feeding and avoid further complications.
Erratic arc
If your arc is erratic, check the condition of the contact tip. If it’s worn or damaged, replace it with a new one. You should also check your welding parameters to make sure they’re correct. Incorrect settings can cause an erratic arc.
What is the role of a 025 Contact Tip in Mig Welding?
Contact tips play a critical role in Mig welding by providing a point of contact between the welding wire and the welding gun’s electrical current. The contact tip is a small, but essential, component that directs the welding wire to the weld joint.
Welding Wire
The welding wire passes through the center of the contact tip and is fed through the gun’s liner to the welding gun’s nozzle. As the electrical current flows through the contact tip, it heats up and melts the welding wire. The molten metal then flows onto the weld joint, creating a strong and durable weld.
Electrical Conductivity
One of the primary functions of the contact tip is to maintain proper electrical conductivity between the welding wire and the gun’s electrical current. However, a worn or damaged contact tip can disrupt this electrical flow, leading to poor weld quality, spatter, or other welding defects.
Therefore, it’s essential to regularly inspect and replace the contact tip as needed to ensure that the electrical current flows smoothly and effectively.
Weld Joint
Another critical role of the contact tip is to guide the welding wire to the weld joint accurately. It helps prevent the welding wire from wandering or wobbling as it passes through the gun’s liner, ensuring that the wire feeds smoothly and consistently.
Final Thoughts
In conclusion, Mig Welder Contact Tips are a critical component in the Mig welding process. Choosing the correct size and material for your contact tips can improve welding efficiency, productivity, and consistency. Regular maintenance, such as proper installation and replacement, can also help to minimize problems and ensure smooth welding operations.