Friction welding, also known as spin welding, is a process used by welders to join two pieces of metal together by applying pressure and heat. It is a popular welding technique for use in many applications because of its ability to create strong and reliable welds. This article will explain how friction welding works and the benefits it provides to welders.
What is Friction Welding
Friction welding is a process in which two pieces of metal are brought into contact and then rotated at high speed while maintaining pressure. Friction causes the metals to heat up, and when the temperature of the metals reaches a certain point, they will begin to fuse. This process takes less time than other forms of welding and produces a stronger bond than other welding methods.
How Friction Welding Works
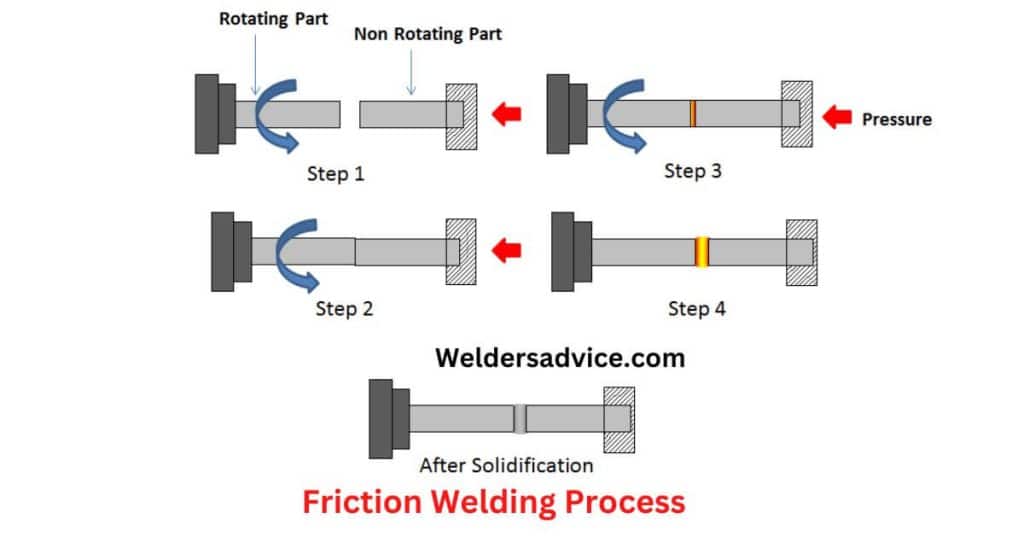
Friction welding is a process whereby two metals are joined together by heat and pressure. The two work pieces are rubbed together at a very high speed and temperature. Melting the surfaces and allowing them to weld together. The weld is strong and reliable and can join harder materials such as stainless steel and aluminium alloys. The process is also very cost-effective compared to other welding methods, as it does not require additional materials or energy.
Friction welding is a quick and easy way to join two metals together. The process is relatively simple and takes less time than other welding methods, making it ideal for quick repairs and production. The resulting weld is strong and reliable, and can be used to join tougher and harder materials. Welder can help you get the job done quickly and accurately, allowing you to get the desired results in less time.
So if you’re looking for a reliable and cost-effective way to join two metals together, friction welding is the answer. This is how Friction Welding Works.
Benefits of Friction Welding
The process is simple and effective, offering many advantages over traditional welding methods. Let’s discuss the various benefits of friction welding with Welder.
Cost-effective
Friction welding is a cost-effective welding process that offers superior results. This process requires comparatively less energy than other welding processes. And the equipment used is comparatively inexpensive. Additionally, the process produces stronger welds than traditional welding processes, using only a few passes. This makes friction welding a great option for cost-effectively joining metals and thermoplastics together.
Weld non weldable materials.
Friction welding can also join materials that are not normally weldable. Stainless steel, aluminum, and titanium are examples of these materials. This makes the process versatile and efficient, as it can join various materials.
High-quality
Another great advantage of friction welding is that it produces high-quality welds with minimal distortion. This eliminates the need for post-welding operations, such as grinding and filing. Additionally, friction welding is a highly automated process, eliminating the need for manual labor and significantly reducing human error risk.
Safe process
Finally, friction welding is a safe process. The process involves very little heat, resulting in a low risk of fire or explosion. Furthermore, the process does not generate any hazardous fumes or gases, making it a great choice for applications where safety is particularly important.
Different Types of Friction Welding
Friction welding is a process that can be used to join dissimilar metals as well as similar metals. This type of welding is used in various industries, including automotive, aerospace, military, and medical. Friction welding can be divided into three types: friction stir welding, flash welding, and ultrasonic welding.
Friction Stir Welding
FSW is a form of friction welding that uses a rotating tool to generate heat and pressure. This process is ideal for joining large pieces of metal with different thicknesses or properties. FSW is commonly used in aerospace, automotive, and military applications.
Flash welding
Flash welding is friction welding that uses an electric arc to create a weld. This process is used to join parts that are too thick or too thin to weld using traditional methods. Flash welding is often used in the manufacturing of large or complex parts.
Ultrasonic welding
Ultrasonic welding is friction welding that uses high-frequency sound waves to create a strong bond between two pieces of metal. It is commonly used in medical devices and other precision instruments. Ultrasonic welding is suitable for joining small and intricate parts.
Disadvantages of Friction Welding
Some disadvantages associated with friction welding should be considered before selecting this welding process for your project.
Brittle and weak
Another disadvantage of friction welding is that it can cause the metal to become brittle and weak. This can occur due to the rapid heating and cooling process, leading to a weakened weld. Consequently, this process is not always the most suitable for structural applications.
limited
Friction welding is limited in its application. The process can only be used on materials with a relatively low melting point. This does not provide much flexibility when welding various materials together.
Time consuming
Another disadvantage of friction welding is its time to complete the process. Unlike traditional welding processes, friction welding requires more time to complete because the material has to be heated to the point where it becomes malleable enough for welding. This can be time consuming and expensive, especially for large welds. In addition, friction welding is unsuitable for some materials due to the higher temperatures required.
High heat
The biggest disadvantage of friction welding is the high heat required to complete the process. While higher temperatures mean better welds, they can also lead to problems with the weld quality and integrity. The heat generated can also affect the surrounding materials and cause them to expand, warp, and melt. This could lead to an inaccurate or weak weld, which could be dangerous if it were to be used in a critical application.
Dangerous
Friction welding can produce a lot of heat and can be dangerous if not done properly. It’s important to use a welder designed to handle the high-heat involved and to take all safety precautions to avoid injury.
Also Read: Salt Water Welding Disadvantages
Things needed for Friction Welding
Here are the essential things you need to get started with friction welding:
High-powered motor
A high-powered motor is essential to generate the heat and pressure needed for friction welding. The motor should reach a speed of at least 15,000 rpm for maximum efficiency.
Friction welding tool
This tool will apply the pressure and heat to the two pieces of metal. The Friction Welder tool is designed to provide the perfect balance of force and heat for friction welding.
Welding gun
The welding gun is used to direct the heat and pressure towards the two pieces of metal. Getting a gun that is the correct size for your specific welding needs is important.
Welding table
A welding table is important to provide a stable, level surface. The Friction Welder table is made from high-grade aluminum for maximum durability and stability.
Welding shield
A welding shield is necessary to protect the welder from the heat and sparks. The Friction Welder shield is designed to provide excellent protection and is made from fire-resistant materials.
Factors that affect friction welding
However, it’s important to understand the factors that affect friction welding to ensure the highest quality welds. The friction welder, the materials being welded, the type of weld being used, and the environment in which the welding is taking place all contribute to the success of a friction weld.
The materials being welded are also important when it comes to friction welding. The materials must be able to withstand the welding process’s heat, pressure and friction. Materials that are too soft or too hard will not be suitable for friction welding. Both the base and filler materials should be chosen for their suitability for the welding process.
The type of weld being used will also affect the quality of the weld. Different types of welds will require different heat, pressure and friction levels. Knowing the right weld for the job is essential to successful friction welding.
Finally, the environment in which the welding occurs is a major factor in friction welding. Dust and contamination can interfere with the welding process, so it’s important to ensure that the environment is as clean as possible. Temperature and humidity can also affect the welding process, so it’s important to ensure that the welding area is sufficiently ventilated and has adequate temperature and humidity control.
Final Thoughts
In conclusion, friction welding is a popular and cost-effective technique that can produce strong and reliable welds. It is a safe process that can join non-weldable materials and is suitable for many applications. The process is relatively simple and only requires a few tools and materials, although factors such as heat and speed can affect the quality of the welds. All in all, friction welding is an excellent and reliable technique for anyone in the welding industry. I hope now you can understand how friction welding works. If you still have any confusion, feel free to comment.